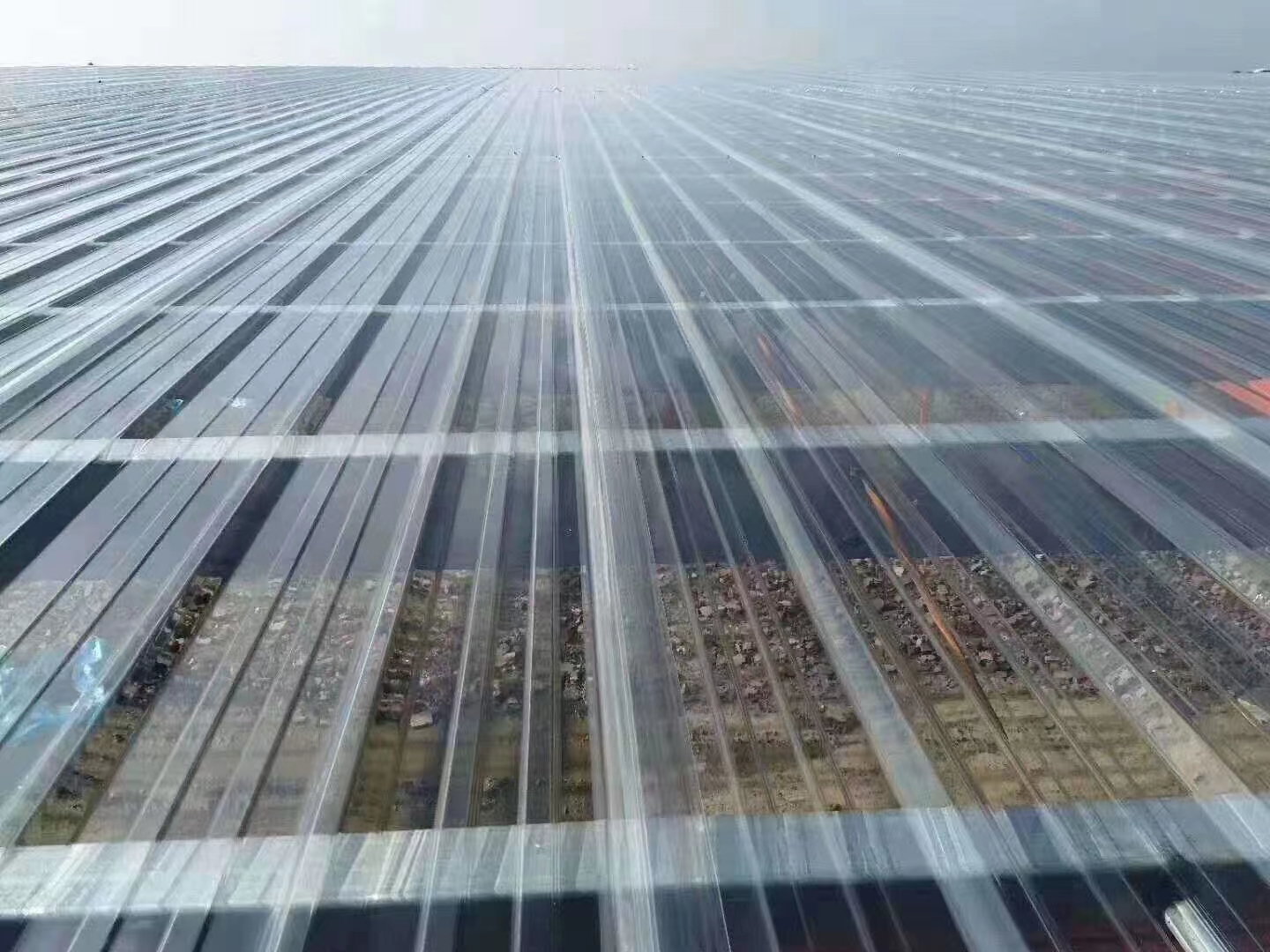
Here´s a comparison table between Polycarbonate Sheets and FRP (Fiberglass Reinforced Plastic) Sheets based on key properties:
Property | Polycarbonate Sheet | FRP Sheet |
---|---|---|
Material Composition | Thermoplastic polymer (Polycarbonate) | Fiberglass reinforced plastic (Resin + Fiberglass) |
Strength | High impact resistance (200x stronger than glass) | Strong and rigid, but less impact-resistant than polycarbonate |
Weight | Lightweight | Lightweight but slightly heavier than polycarbonate |
Transparency | High transparency (up to 90%) | Can be translucent, transparent, or opaque depending on the type |
UV Resistance | Requires UV coating for outdoor use | Naturally UV-resistant, does not degrade easily |
Fire Resistance | High fire resistance, self-extinguishing | Fire retardant options available but varies by resin type |
Corrosion Resistance | Good chemical resistance, but may degrade with time | Excellent corrosion resistance, ideal for harsh environments |
Weather Resistance | Can become brittle over time with UV exposure | Highly durable against weather and temperature variations |
Flexibility | Highly flexible, can be bent without breaking | Rigid and less flexible than polycarbonate |
Thermal Insulation | Good insulation properties | Moderate insulation properties |
Lifespan | 10–15 years (depending on UV protection) | 20+ years with proper maintenance |
Applications | Skylights, greenhouses, safety shields, roofing | Industrial roofing, cooling towers, chemical plants, warehouses |
Cost | More expensive than FRP in some cases | Generally more cost-effective for large applications |
Which One to Choose?
Choose Polycarbonate if you need high impact resistance, flexibility, and optical clarity (e.g., skylights, greenhouses, safety barriers).
Choose FRP Sheet if you need superior corrosion resistance, durability, and long-term performance in industrial and harsh environments (e.g., chemical plants, cooling towers, and warehouses).
Let me know if you need further customization or details!